More reliable bonds for power semiconductors made possible with a novel way to assess wire bonding materials
To understand the quality of a wire bond with a semiconductor chip, they are subjected to shear tests at the contact point where the wire meets the chip: A chisel shears off these so-called wedges, and the necessary force and resulting damage is analyzed. To learn more about what happens during shearing, researchers from the Technical University of Berlin and Fraunhofer IZM came up with an innovative simulation of the mechanical processes at work. This allows them to understand how newer and more durable wire types affect the behavior of the material and the processes and to produce a more objective and reliable assessment of the bonding quality of such novel materials.
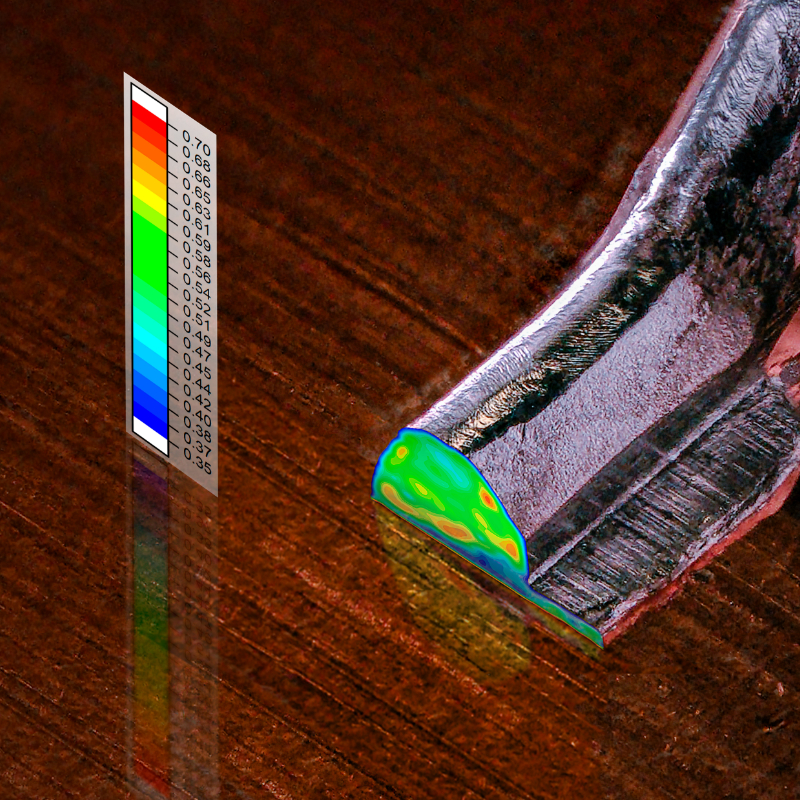
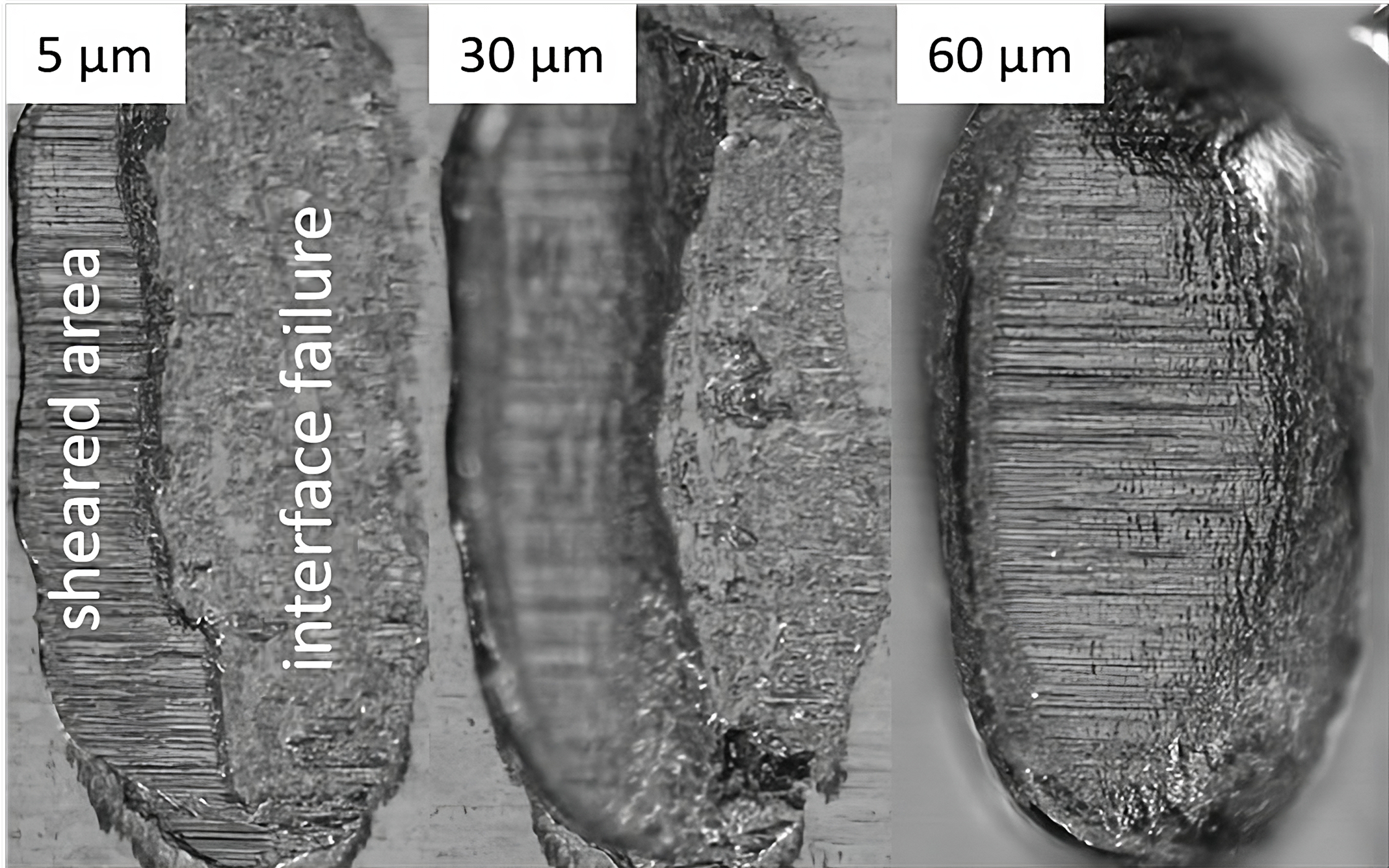
Wire bonding with aluminum wires remains the most popular technology for creating electrical contacts on semiconductor chips in microelectronics or power electronics systems. It is cost effective and can be extensively automated despite the complexity of the process. The quality of the wire bond contact on the chip surface has a direct impact on the life expectancy of the finished system. This is why intensive efforts are still under way worldwide to develop new materials and interconnection techniques despite the decades of experience with wire bonding. Scientists from Fraunhofer IZM and TU Berlin have been part of this undertaking for more than 20 years and are among the world’s leading experts in this fundamental part of microelectronics technology.
More durable materials for thick wire bonding
Novel wire types that wrap a copper core in aluminum or that use aluminum-magnesium alloys promise to be far more durable than regular aluminum-only materials. When subjected to shear tests, the resulting damage patterns also differs from their aluminum counterparts. Called shear codes, these patterns and the shear force needed to create them can tell researchers a lot about the bond quality of the wedge. The researchers would compare how much of the bond’s contact surface is covered by the sheared wedge with the shear force exerted, and depending on how long the wedge is before it detaches from the substrate (euphemistically called the lift-off), the material is given a shear code between 1 and 4. But these shear codes, originally defined for standard thick aluminum wires, do not translate well to more novel materials: The material tends to fail or lift off during shearing not in the wedge of extremely hard wire, but sometimes in the softer chip or substrate metallization layer. For standard quality checks, this would be recorded as an unacceptable early lift-off and taken to mean that the bond quality was insufficient. The old shear codes therefore allow no meaningful statement about the quality of the bonds made with the newer materials. No universally acceptable guidelines exist year for interpreting shear tests with novel wire types, which leaves a major question mark over one important element of quality management.
Reinterpreting shear codes for novel wire types
The specialists at Fraunhofer IZM and the Technical University of Berlin set out to remedy this situation. They subjected a number of materials and alloys to a battery of shear tests and created a so-called metallographic analysis of the resulting damage patterns during different points of the shearing process. For their substrate, the researchers picked highly pure copper, which is known to be harder than the tested wire materials. This meant that the shearing damage would be concentrated on the wedge and not be obscured by a failure of the substrate. For their simulation of the damage mechanics in the shear tests, the necessary properties of the materials were established in actual tensile tests and simulations using specialized open source software. It allowed the researchers to establish the damage mechanics during shear testing in relation to the chosen wire material and any preexisting deformation from the original bonding process. The results obtained from this were compared to the empirical shear tests, giving the researchers a better insight into what happens to different materials and material combinations during shearing.
Applying the insights to other use cases
The damage mechanics simulation for shear testing wire bonds that was developed in the project can now be used in other applications. It can help rethink lifecycle assessments in bonding and interconnection technology and facilitate the necessary simulation work. The data also offers a better insight into the complex mechanisms at work when different forces interact with each other.
The Scherwedge project ran from late 2020 to early 2023 and was made possible with €200,000 in funding from the German Research Foundation DFG (project ID: 456843234).
Additional publications
Kuttler, S., Wittler, O. & Schneider-Ramelow, M. Behavior of Different Ultrasonically
Bonded Aluminum Heavy Wires in the Shear Test. J. Electron. Mater. doi:
10.1007/s11664-024-11131-8, (2024)
https://link.springer.com/article/10.1007/s11664-024-11131-8
S. Kuttler, O. Wittler, M. Schneider-Ramelow, Numerical Simulation of a Wire Bond
Shear Test Using Nonlinear Adaptive Remeshing. EuroSimE Proceedings, vol. 23, pp. 1-3, doi:
10.1109/EuroSimE54907.2022.9758846, (2022)
https://ieeexplore.ieee.org/document/9758846
S. Kuttler, B. E. Abali and O. Wittler, "Determination of Lemaitre Damage Parameters for Al H11 Wire Material," EuroSimE Proceedings, pp. 1-3, doi:
10.1109/EuroSimE56861.2023.10100825. (2023)
https://ieeexplore.ieee.org/document/10100825
Last modified: